- Vacuum furnace & oven
- Annealing Furnace & Oven
- Tempering furnace & oven
-
Carburizing furnace & Ovens
-
Bell Type Furnace
-
Pit Type Furnace & Well Type Furnace
-
Box Furnace & Chamber Furnace
-
Car Bottom Furnace & Bogie Hearth Furnace
-
Nitriding furnace & Ovens
-
Melting furnace & Ovens
- Quenching furnace & Ovens
-
Rapid quenching furnace & Ovens
- Forging furnace & Ovens
- Bright heat treatment furnace & Ovens
Hooded Vacuum Furnace & Ovens
Heat treatment furnace manufacturer,Jiangsu Hongtai Industrial Furnace Technology Co., Ltd
Shroud type vacuum furnace: Mainly for metal machine parts, strip steel, copper strip, wind power flanges, slewing bearings, valves, bearings, wheels and other large alloy steel machine parts for bright heat treatment.
Hooded Vacuum Furnace & Ovens
Flexible Loading • Superior Vacuum Control • Efficient Operation
Product Introduction
Our Hooded Vacuum Furnace & Ovens represent the pinnacle of flexible industrial vacuum heat treatment technology, specifically engineered for batch processing, research applications, and specialized manufacturing requiring versatile loading configurations and superior vacuum performance. The unique hooded design enables convenient access to the heating chamber while maintaining excellent vacuum integrity and temperature control. This advanced equipment is extensively utilized across research institutions, specialty manufacturing, aerospace components, and precision engineering sectors, serving as critical equipment for vacuum annealing, brazing, sintering, and specialized heat treatment processes that demand exceptional flexibility and reliability.
Core Advantages That Define Flexible Vacuum Excellence
- Flexible Hooded Design: Removable hood configuration enables easy access to heating chamber for complex workpiece loading and fixture arrangements with excellent vacuum sealing performance
- Superior Vacuum Performance: Advanced vacuum systems achieving ultimate vacuum levels of 10^-4 to 10^-6 Pa with rapid evacuation capabilities for efficient batch processing
- Versatile Process Capabilities: Single equipment capable of vacuum annealing, brazing, sintering, degassing, and specialized research applications with programmable control systems
- Efficient Batch Processing: Optimized chamber design for maximum workpiece capacity while maintaining temperature uniformity and vacuum integrity throughout the load
- Advanced Control Systems: Sophisticated PLC control with touchscreen interface, recipe management, and comprehensive data logging for process documentation
- Robust Safety Features: Comprehensive safety systems including hood position monitoring, vacuum interlocks, temperature limits, and emergency shutdown capabilities
- Customizable Configurations: Flexible design options for chamber sizes, heating elements, vacuum systems, and control features to meet specific application requirements
Technical Specifications
Parameter | Unit | Range/Value | Notes |
---|---|---|---|
Maximum Working Temperature | °C | 600 - 1300 | Application-specific configuration |
Ultimate Vacuum Level | Pa | 6.7×10^-4 - 6.7×10^-6 | High-performance vacuum systems |
Rated Power | KW | 25 - 200 | Efficient heating systems |
Working Chamber (Dia. × Height) | mm | φ500×400 to φ1500×1200 | Custom sizes available |
Temperature Uniformity | °C | ±2 (typical) | Multi-zone heating control |
Control Accuracy | °C | ±1 | Advanced PID control |
Pump-down Time | min | 15 - 45 | Rapid evacuation capability |
Heating Rate | °C/min | 2 - 15 (adjustable) | Programmable heating curves |
Cooling Method | - | Natural/Gas quench/Fan cooling | Multiple cooling options |
Hood Operation | - | Manual/Semi-automatic | Flexible access configuration |
Vacuum Pump System | - | Rotary + Diffusion/Turbo | High vacuum performance |
Control System | - | PLC + Touchscreen HMI | Advanced automation |
Working Principle
The working principle of a vacuum heat treatment furnace is primarily based on heating and cooling materials in a vacuum environment to achieve specific heat treatment effects. Unlike traditional heat treatment furnaces, vacuum furnaces remove air and other gases from the furnace chamber by vacuuming, thereby preventing the workpiece from reacting with active gases such as oxygen and nitrogen at high temperatures, effectively preventing oxidation, decarburization, and contamination. This results in a clean surface for the treated workpiece, eliminating the need for subsequent machining or surface treatment, and significantly improving product quality and production efficiency.
The furnace body typically contains heating elements (such as graphite, molybdenum, or tungsten heaters) and insulation layers. Under the action of a vacuum pump system (usually composed of mechanical pumps, Roots pumps, and diffusion pumps or turbomolecular pumps), the pressure in the furnace chamber can reach extremely low vacuum levels (e.g., 10^-4 to 10^-6 Pa). The workpiece is placed in the heating zone and heated to a preset temperature by radiation or convection. A precise temperature control system (such as a PID controller) ensures the uniformity and stability of the heating process.
After the heating and holding stages, the furnace undergoes cooling. Cooling methods vary and can include natural cooling or rapid cooling (gas quenching) by introducing inert gases (such as nitrogen or argon) to meet the cooling rate requirements of different materials and processes. Rapid cooling is usually achieved through internal circulation fans and heat exchangers, ensuring that the workpiece reaches the desired temperature in a short time and obtains the ideal microstructure and properties. The entire process is automatically managed by an advanced PLC control system, achieving precise temperature, pressure, and time control, and recording all process data to ensure process repeatability and traceability.
Process Flow
Hood Removal & Loading
Remove hood to access heating chamber and load workpieces using appropriate fixtures and spacing for optimal heat distribution and vacuum performance.
Hood Installation & Sealing
Install hood with precision sealing mechanisms and initiate vacuum evacuation to achieve required vacuum level for contamination-free processing.
Process Execution
Execute programmed heating cycle with precise temperature control and monitoring, maintaining optimal vacuum and thermal conditions throughout the process.
Cooling & Unloading
Controlled cooling with optional gas backfill, followed by hood removal and workpiece unloading for quality assessment and further processing.
Solving Customer Pain Points
Complex Loading Requirements
Our hooded design provides excellent access to the heating chamber, enabling complex workpiece arrangements and fixture configurations that would be difficult with other furnace types.
Batch Processing Efficiency
Optimized chamber design maximizes workpiece capacity while maintaining temperature uniformity and vacuum integrity, improving batch processing efficiency and throughput.
Research Flexibility
Versatile configuration options and easy access design make it ideal for research applications requiring frequent setup changes and experimental flexibility.
Operation Simplicity
Intuitive touchscreen interface with recipe management simplifies operation procedures, reduces training requirements, and ensures consistent results across different operators.
Process Documentation
Comprehensive data logging and reporting capabilities meet regulatory requirements and research documentation needs with automatic record keeping and traceability.
Maintenance Accessibility
Hooded design provides excellent access for maintenance and service operations, reducing downtime and maintenance costs while ensuring reliable operation.
Customer Success Stories
A leading aerospace research facility achieved a 60% improvement in experimental throughput and 40% reduction in setup time after implementing our hooded vacuum furnace system, enabling breakthrough research in advanced materials and manufacturing processes.
Customized Services
We provide comprehensive customization services from equipment design, manufacturing, installation, and commissioning to after-sales maintenance, fully meeting customers' personalized requirements. Whether for specialized research applications, unique loading configurations, or specific process requirements, we can provide professional solutions to ensure optimal performance and integration with your production environment.
Related Keywords
hooded vacuum furnace, bell vacuum furnace, vacuum oven, batch vacuum furnace, flexible vacuum heat treatment, vacuum annealing, vacuum brazing, vacuum sintering, custom vacuum solutions, research vacuum equipment, aerospace heat treatment, precision manufacturing equipment, experimental vacuum processing
Hooded Vacuum Thermal Processing Systems: Technical Specifications
1. Core Operating Principles
Hooded Vacuum Furnace & Oven
Utilizes a suspended refractory metal hood that descends to form an isolated processing chamber. During heat treatment of aircraft turbine blades, the hood’s radiation shielding maintains thermal uniformity while enabling rapid inert gas purges between batches – critical for preventing titanium embrittlement.
Hooded Vacuum Oven
Incorporates a gas-knife sealing system where nitrogen jets create a dynamic barrier at the hood-base interface. This allows continuous moisture extraction in MEMS gyroscope production without atmospheric exposure, achieving <50ppm residual humidity.
Hooded Heat Treatment Furnace
Employs segmented hood heating with independent radiative control. For wind turbine gear processing, the upper hood zone maintains austenitizing temperature while the lower zone precisely regulates quenching gas flow to preserve core toughness.
2. Advanced Process Methodologies
- Aerospace Components: Sequential hooded vacuum annealing eliminates stress in 3D-printed rocket nozzles through controlled thermal gradient reversal.
- Medical Devices: Cobalt-chromium hip implants attain oxide-free surfaces via the hooded furnace’s dual-phase cooling protocol.
- Automotive: Aluminum die-cast bodies undergo distortion-free solution treatment using the hood’s multi-zone temperature profiling.
3. Industrial Value Proposition
The process isolation capability of hooded systems delivers:
- 40% reduction in aerospace titanium processing costs (eliminating intermediate cleaning)
- 300% extended tool life in medical implant manufacturing (through controlled surface finishing)
- 18% energy savings in automotive heat treatment (via precise atmosphere management)
Vacuum furnace, that is, in the furnace cavity of this specific space using a vacuum system (by the vacuum pump, vacuum measurement devices, vacuum valves and other components carefully assembled) will be part of the furnace cavity material discharge, so that the pressure in the furnace cavity is less than a standard atmospheric pressure, the furnace cavity space so as to realize the vacuum state, which is the vacuum furnace.
Product Description:
This is a device for heating in a vacuum environment. In the metal shell or quartz glass sealed furnace chamber with piping and high vacuum pump system connection. The vacuum degree of the furnace chamber can be up to 133×(10-2~10-4) Pa. The heating system in the furnace can be directly heated by resistance wire (such as tungsten wire), or can be heated by high-frequency induction. The temperature can reach about 3000℃. It is mainly used for ceramic firing, vacuum smelting, degassing and annealing of electric vacuum parts, brazing of metal parts, and ceramic-metal sealing.
Advantages
(1) The oxidation and decarburization of the surface of the workpiece during the heating process are eliminated, and a clean surface without deterioration layer can be obtained. This improves the cutting performance of tools that are only ground on one side during sharpening (e.g., twist drills are ground so that the decarburized layer on the surface of the grooves is directly exposed to the cutting edge).
2)No need for three waste treatment.
(3) Furnace temperature determination, monitoring and control accuracy is significantly improved. Thermocouple indication value and furnace temperature temperature to ± 1.5 ° c. But the temperature difference between different parts of a large number of workpieces in the furnace is large, if the use of dilute gas forced circulation, can still be controlled in the range of ± 5 ° c temperature difference.
(4) high degree of mechanical and electrical integration. On the basis of temperature measurement and control accuracy, workpiece movement, air pressure adjustment, power regulation can be pre-programmed settings, according to the step-by-step implementation of quenching and tempering.
(5) Energy consumption is significantly lower than the salt bath furnace. Modern advanced vacuum oven heating chamber using thermal insulation materials made of heat-insulating walls and barriers, can be highly concentrated in the heating chamber of electric energy, energy saving effect is significant.
Function
Vacuum quenching (tempering, annealing) is a treatment method to achieve the expected performance by heating and cooling the material or parts under vacuum according to the process protocol.
Vacuum brazing is a welding process in which a group of welded parts is heated to a temperature above the melting point of the filler metal but below the melting point of the base metal in a vacuum state, and a weld is formed with the help of the filler metal's wetting and flowing of the base metal (brazing temperatures vary depending on the material).
Vacuum sintering that is, in a vacuum state, the metal powder products heated, so that adjacent metal powder grains through adhesion and diffusion and sintered into parts of a method.
Vacuum magnetization is mainly applied to the magnetization treatment of metal materials.
Classification
Vacuum furnace, i.e. vacuum heat treatment furnace, is distinguished according to the application equipment, which probably contains the following types:
Vacuum quenching furnace, vacuum brazing furnace, vacuum annealing furnace, vacuum magnetizing furnace, vacuum tempering furnace, vacuum sintering furnace, vacuum diffusion welding furnace, vacuum carburizing furnace and so on.
Vacuum furnace is divided into vacuum resistance furnace, vacuum induction furnace, vacuum arc furnace, vacuum self-consumption arc furnace, electron beam furnace (also known as electron bombardment furnace) and plasma furnace, etc. according to the heating method.
Structure
Vacuum furnace is generally composed of mainframe, furnace chamber, electric heating device, sealed shell, vacuum system, power supply system, temperature control system and outside the furnace transportation vehicle and so on. The sealed shell is welded with carbon steel or stainless steel, and the joint surfaces of the removable parts are sealed with vacuum sealing materials. In order to prevent the furnace shell deformation and sealing material heat deterioration, the furnace shell is generally water-cooled or air-cooled cooling. The furnace chamber is located in the sealed furnace shell. Depending on the purpose of the furnace, the interior of the furnace chamber is equipped with different types of heating elements, such as resistors, induction coils, electrodes and electron guns. Vacuum furnaces for melting metals are equipped with crucibles in the furnace chamber, and some are also equipped with automatic pouring devices and robots for loading and unloading materials. The vacuum system is mainly composed of vacuum pumps, vacuum valves and vacuum gauges.
Application
1.High-pressure high-flow rate gas quenching vacuum furnace
Mainly used for cold and hot work mold steel, high-speed steel, elastic alloys, high-temperature alloys, stainless steel, titanium alloys, magnetic materials and other materials, vacuum heat treatment.
2 double chamber high pressure gas quenching vacuum furnace
Mainly used for high pressure gas quenching of cold and hot working die steel, high-speed steel, elastic alloy, high temperature alloy, stainless steel, titanium alloy, magnetic materials and other materials, as well as vacuum sintering, vacuum brazing and other processes.
3.Double-chamber oil quenching gas-cooled vacuum furnace
It is mainly applied to bright quenching of tool steel, mold steel, bearing steel, spring steel and other materials.
4.Vacuum aluminum brazing furnace
Mainly applicable to automobile radiator, air conditioner evaporator, condenser, intercooler, radar grid antenna, waveguide, and all kinds of plate warping or tube sheet type heat exchanger vacuum welding.
5.Vacuum high temperature brazing furnace
It is mainly used for vacuum brazing of stainless steel, high temperature alloy, hard alloy, non-ferrous metal and other materials.
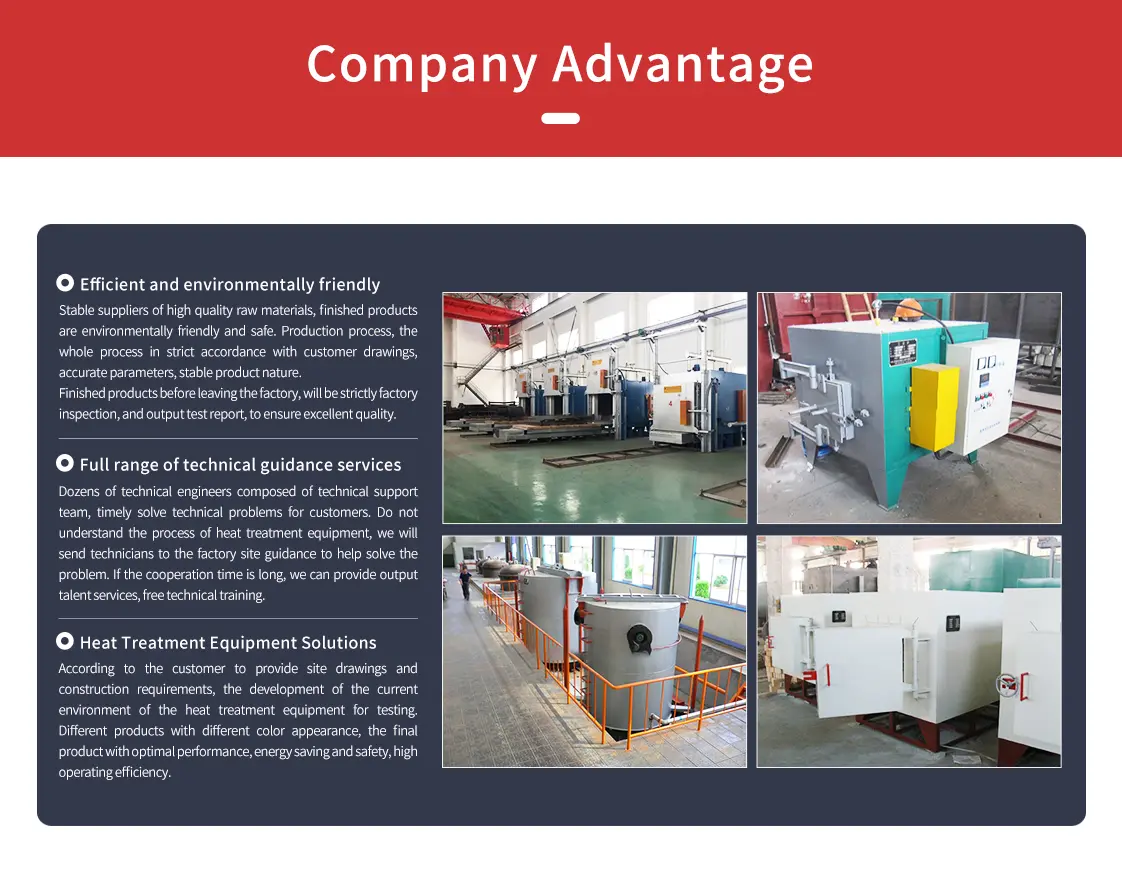
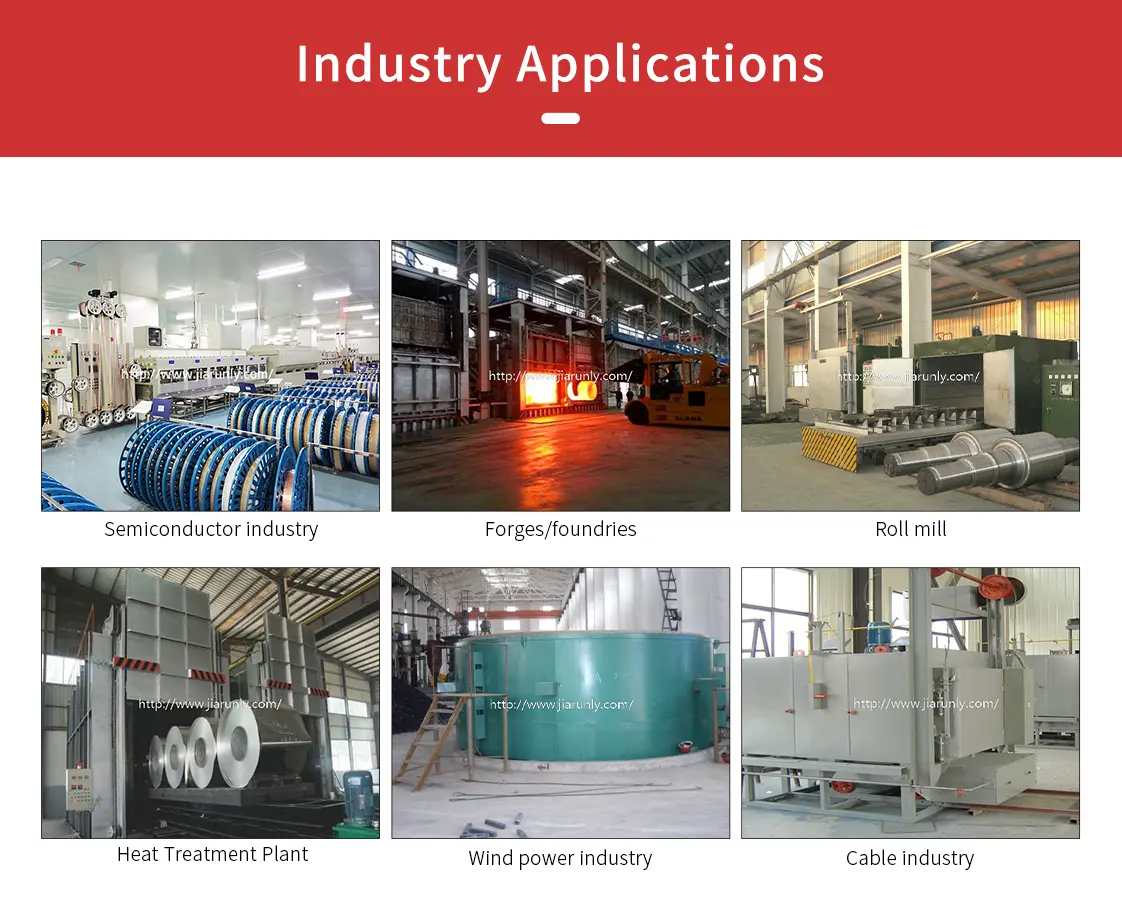
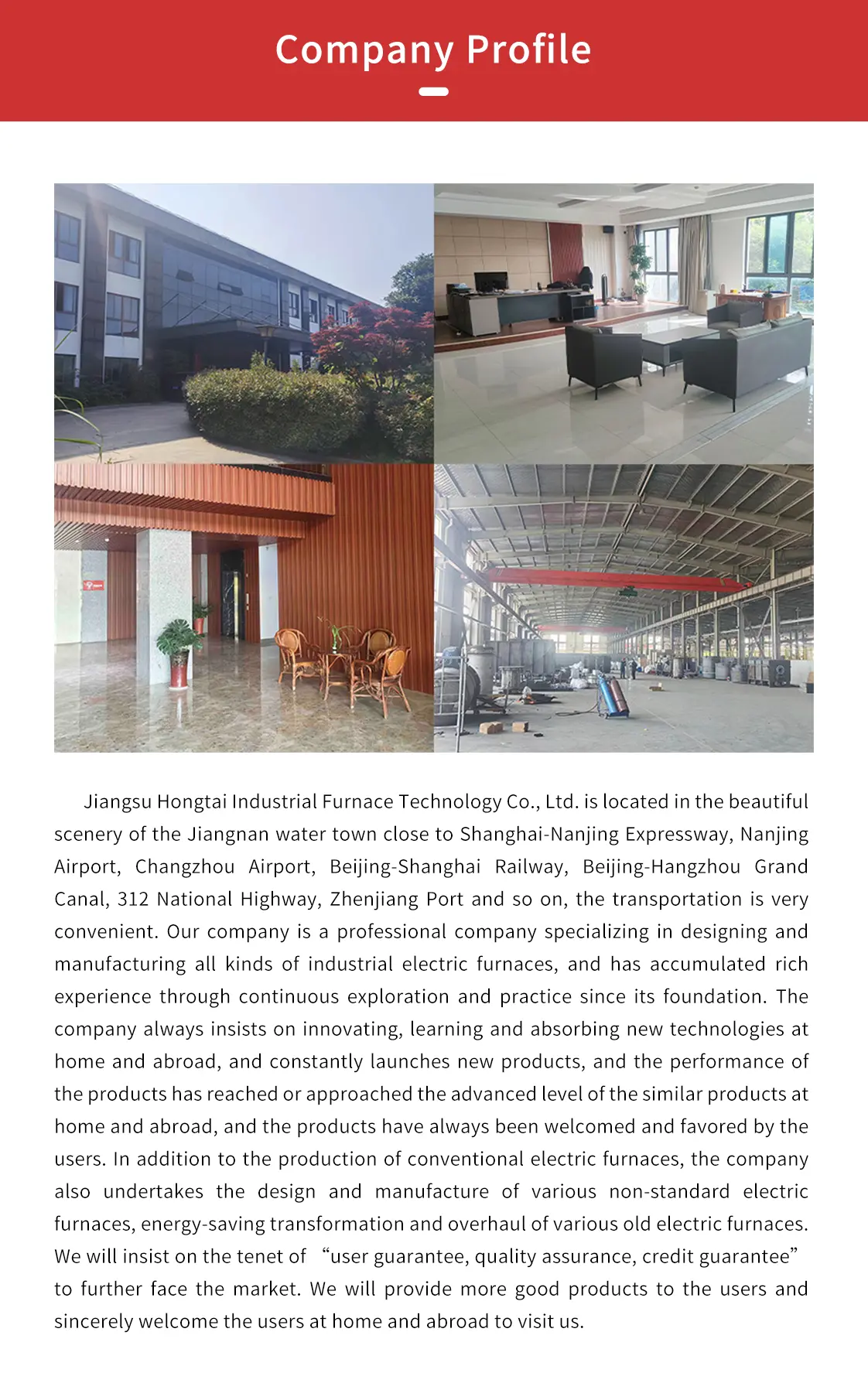
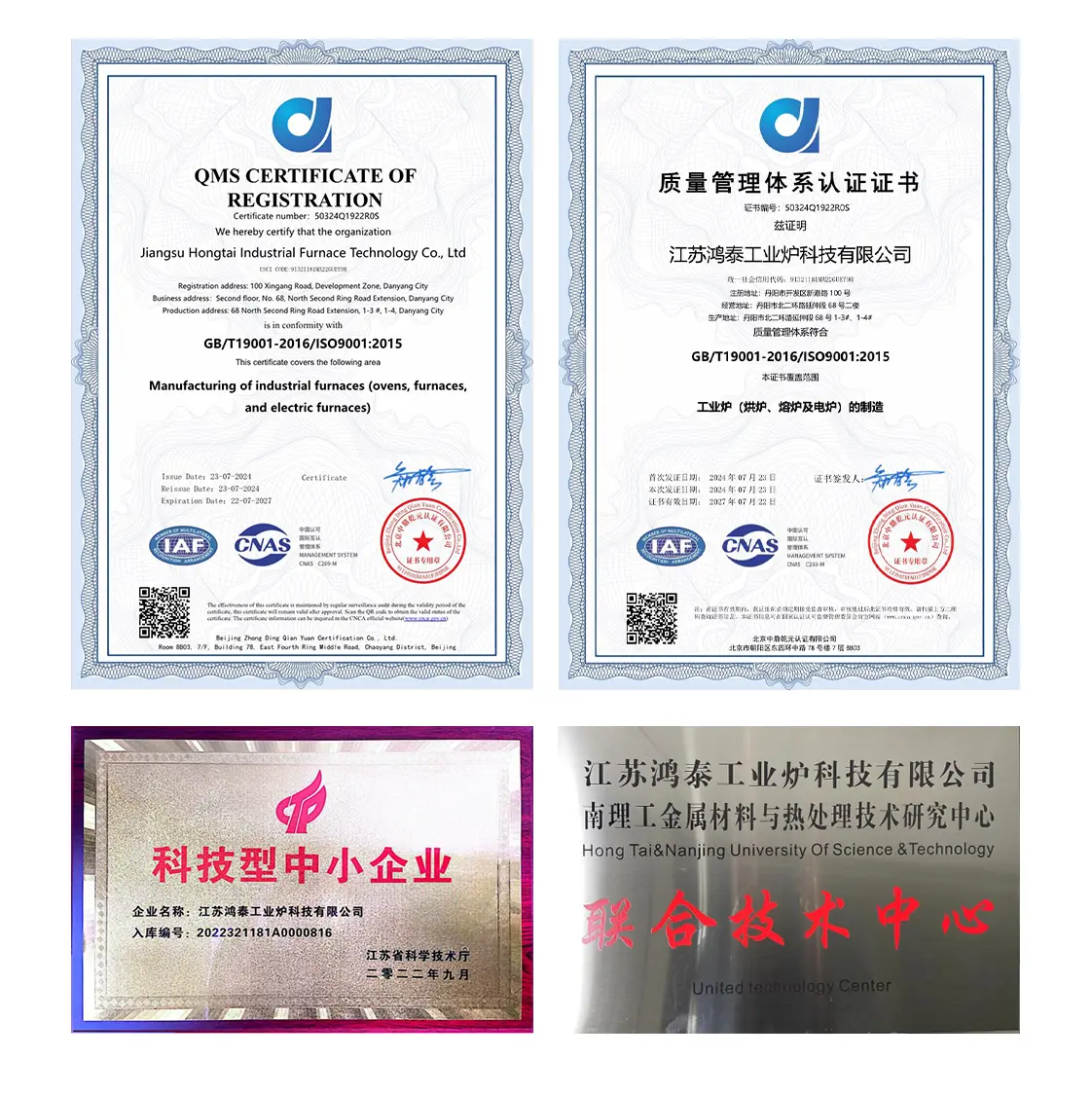